News
New discoveries to minimise deterioration of materials through Directed Energy Deposition published in Nature Communications.
26 February 2024
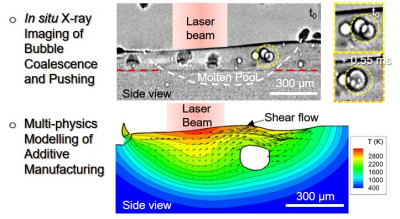
Directed Energy Deposition is a manufacturing process in which materials are melted and fused onto surfaces and into desired shapes, in a layer-by-layer process. It is often used in repairs, such as in the repair of damaged jet turbine blades, and in the automotive, marine, aerospace and biomedical fields.
However, its widespread use in industry has been limited by porosity (the development of pores) which occurs during the process. Tiny air bubbles are created, affecting the long-term performance and lifespan of the material, and having safety implications.
Until now, how this porosity develops remained unclear. This study, conducted by Dr Chinnapat Panwisawas at Queen Mary University of London, used in-situ X-ray imaging validated by multi-physics modelling, to outline five mechanisms which contribute to the pore formation, movement and growth.
Bubbles from gas atomised powder enter the melt pool, and then migrate circularly or laterally
Small bubbles can escape from the pool surface, coalesce into larger bubbles, or be entrapped by solidification fronts. Larger coalesced bubbles can remain in the pool for long periods, pushed by the solid/liquid interface. Marangoni surface shear flow (the movement of fluid as material melts and pools) overcomes buoyancy, keeping larger bubbles from popping out. Once large bubbles reach critical sizes they escape from the pool surface or are trapped in DED tracks
The discovery of these mechanisms can now guide the development of pore minimising strategies, leading to innovative regenerative and repair technologies.
"This knowledge is crucial for unlocking the full potential of DED. By minimising porosity, we can improve the mechanical properties of components, making DED a viable option for safety-critical applications ultimately leading to the production of stronger, safer, and more reliable components across various industries" said Dr Chinnapat Panwisawas, Senior Lecturer in Materials and Solid Mechanics at Queen Mary’s School of Engineering and Materials Science.
The study was an international collaboration with University College London, Research Complex at Harwell (UK), ESRF-The European Synchrotron (France), RMIT (Australia), Diamond Light Source (UK), Rolls Royce plc (UK) and Shimane University (Japan).
You can read the full publication, Pore evolution mechanisms during directed energy deposition additive manu… and view a video of their findings in the LinkedIn post below.
Contact: | Chinnapat Panwisawas |
Tel: | 07551 428989 |
Email: | c.panwisawas@qmul.ac.uk |
Website: | |
People: | |
Research Centre: |